This week (October 6-October 12, 2013) is Fire Prevention Week. It is a good time to remind ourselves to check that we are following all the proper fire prevention procedures, whether we work in theatre, an independent shop, or at home.
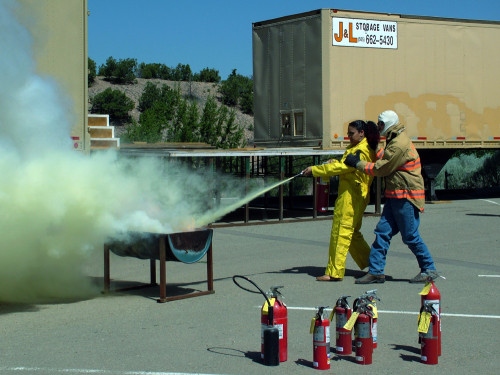
Fires happen. We should not pretend that they are a thing of the past, or that our laws and technology protect us. Every year, Patrick Hudson of OffstageJobs.com reminds us how many fires (that we hear of) happen in the entertainment industry; in 2012, there were at least 14. His posts do a good job of reminding us what the proper procedures are. And in case you think they can’t happen to you, he reminds us that the Iroquois Theatre thought the same (go read those articles now; I’ll wait). Despite its boast of being “fireproof” in a city with one of the strictest fire codes in the world, it caught fire in 1903 and killed 602 people. This was not the result of some grand failure, but rather a whole lot of little things that could have been avoided: exit doors were unmarked or blocked, lighting fixtures were in the path of the fire curtain, the scenery was not adequately flame-proofed, etc. Most of these were violations of existing fire code, rather than the lack of knowledge of how to prevent fires.
So while props people are typically not in charge of maintaining many of these things, as a member of the production team, we can still monitor them. If management or producers are pushing for unsafe practices (like covering the exit signs, or disabling the fire curtain), we can stand with the rest of the technicians so they do not need to fight the battle alone. We can keep our props out of stairwells and maintain clear egress paths through our storage areas. If we have prop fire extinguishers, keep them labelled well and far away from real fire extinguishers. Leave flammables in the flammables cabinet. If you are not aware of all the regulations and procedures to follow, Fire Prevention Week is a good time to brush up.
And if you work in your rental home or apartment (and even if you don’t), get renter’s insurance. My wife and I lived through a fire that destroyed our whole apartment building. It’s traumatizing enough without having to worry about all your stuff and where you’re going to live. You may not think you have enough stuff to make it worthwhile, but the value of all your little odds and ends adds up quick. Renter’s insurance is much more than just replacing your stuff; ours also sent movers to salvage and clean what they could while housing us in a temporary apartment. I only had to miss one day of work, which was important because I was freelancing at the time, and paid hourly. Anyone in the building without insurance had to scramble to find a place to sleep that same day, as well as take time off work to haul all their belongings out before they were damaged further or looted.
So take this week to double-check that you are doing all you can to prevent fires and are prepared to deal with one should it occur, both at work and at home. You’ll be glad you did.