I am currently working as props master on Crazy for You at Elon University. In one of the musical numbers, twelve showgirls dance around the main character while talking on the phone. The show is set in the early 1930s, so that is twelve candlestick phones needed (all of them painted pink). If you’ve ever had to get candlestick phones, you know that the real ones are prohibitively expensive, and even the replicas are too expensive when twelve are needed. I decided I would make them all (which is what most theatres do).
Most hand-built candlestick phones I’ve seen have a pretty simple base, and I wanted to try for something a bit more interesting and realistic. Since these were just being used during a dance number, the dial didn’t need to work. It looked like I could sculpt the base as a solid object and than just vacuum form twelve copies. The only problem? I don’t have a vacuum forming machine.
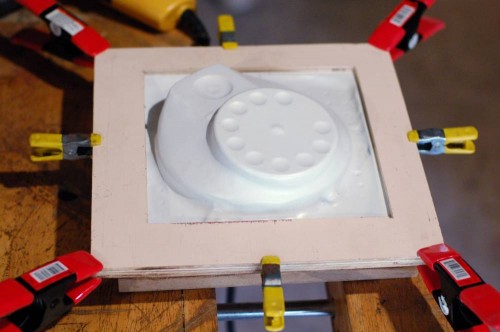
I ended up assembling a very small and fairly weak vacuum forming system out of tools I already had and scrap materials which were laying around. Other than my time, the cost was free. I was able to make all the phone bases I needed though the process was a bit inelegant at times. I like what vacuum forming can accomplish, and I think I may spend some more time (and maybe even some money) making a more usable vacuum former after this show opens, but it was nice to be up and running without too much investment on my part.
I have posted an Instructable on how I built my free vacuum forming machine if anyone else is interested in how this all works. I also have a video of how it works and what it looks like when it’s being used: