Last week, I showed off some giant champagne bottles I made, and mentioned that they would act as the barrels of some cannons I was also building at the Santa Fe Opera. Today, I will show you the actual cannon barrels I made. We needed four cannons, so that meant four barrels.
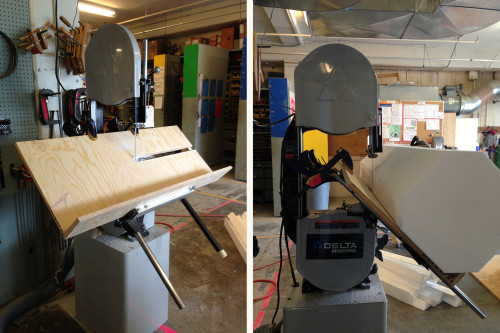
I made the barrels out of foam to keep them lightweight; the Santa Fe Opera runs their shows in repertory, so any savings in weight is much appreciated by the running crew, who have to move all the props from the basement to the stage on a daily basis. I whipped up a quick jig for the bandsaw to cut the corners from the blocks of foam I got. This meant less time turning, less dust, and it allowed the foam to actually fit on the lathe.
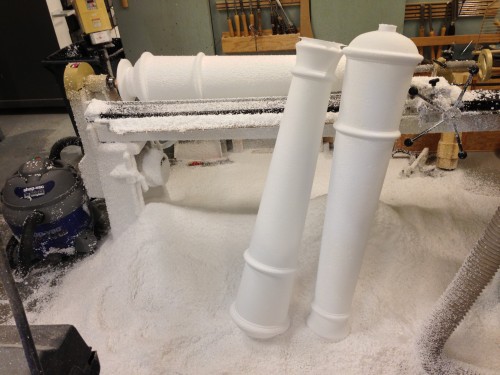
I designed a full-size template of the shape of the barrels based on the designer’s sketches and my own research. I could also use this template as a pattern on the lathe to make all four barrels exactly the same as each other. Turning foam on the lathe is fun and easy, but it makes a gigantic mess.
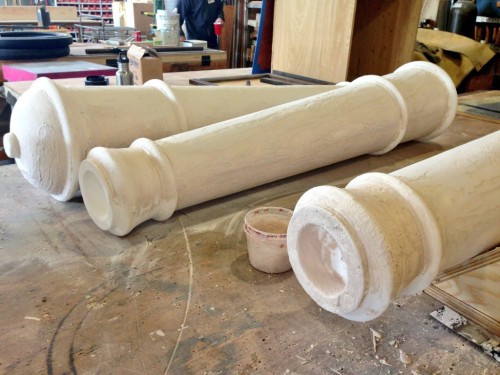
After the barrels were taken off the lathe, I began the long and laborious process of coating and sanding them. The designer wanted them to look like smooth brass without any distressing, so they needed to be absolutely flawless. I used Aqua Resin, which provided a sandable hard coat with far less toxicity than Bondo. I spent nearly a week just coating and sanding all these guys.
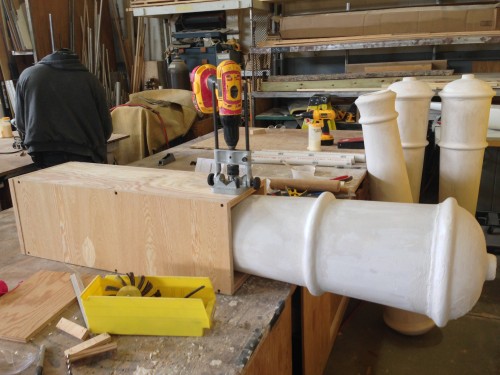
I built a jig so I could hold the barrel and a cordless drill perpendicular to each other. This provided a pilot hole for the trunnion I would add; the trunnion would be a piece of PVC pipe which would hold the cannon on the carriage and allow it to pivot up and down.
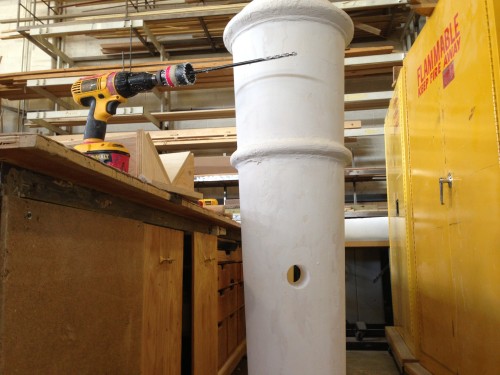
With the pilot hole drilled, I switched to a hole saw that was closer to the size of the PVC pipe. You can see in the photo above that I have an extra long pilot bit on the hole saw. This bit was long enough to pop out the other side of the barrel so I could be sure that the hole saw would exit in exactly the right place.
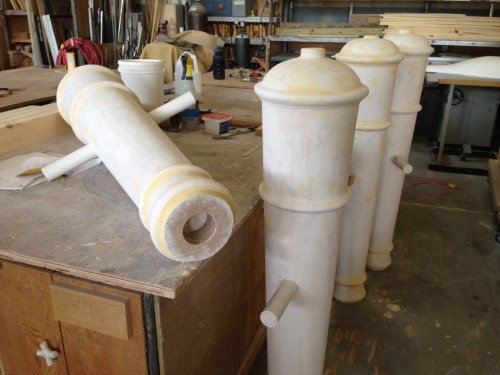
I pushed the sections of PVC pipe through the hole and capped off the ends to make them look like a solid bar. I also added some lauan rings to the ends of the barrels to help reinforce them when they were standing up.
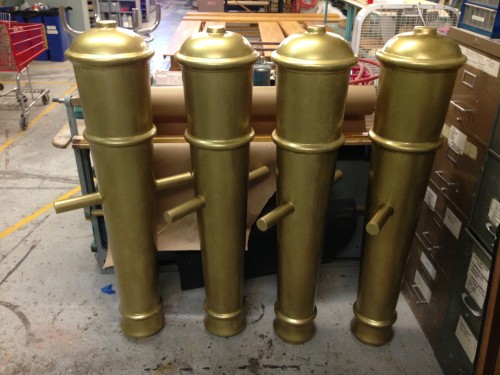
With the barrels finished, I handed them off to the painters, who gave them the great brass paint treatment that you see above. In a few days, I’ll post about how I built the carriages to these cannons, and you can see pictures of the final piece.